Обработка деталей на токарных станках: основные методы и техники
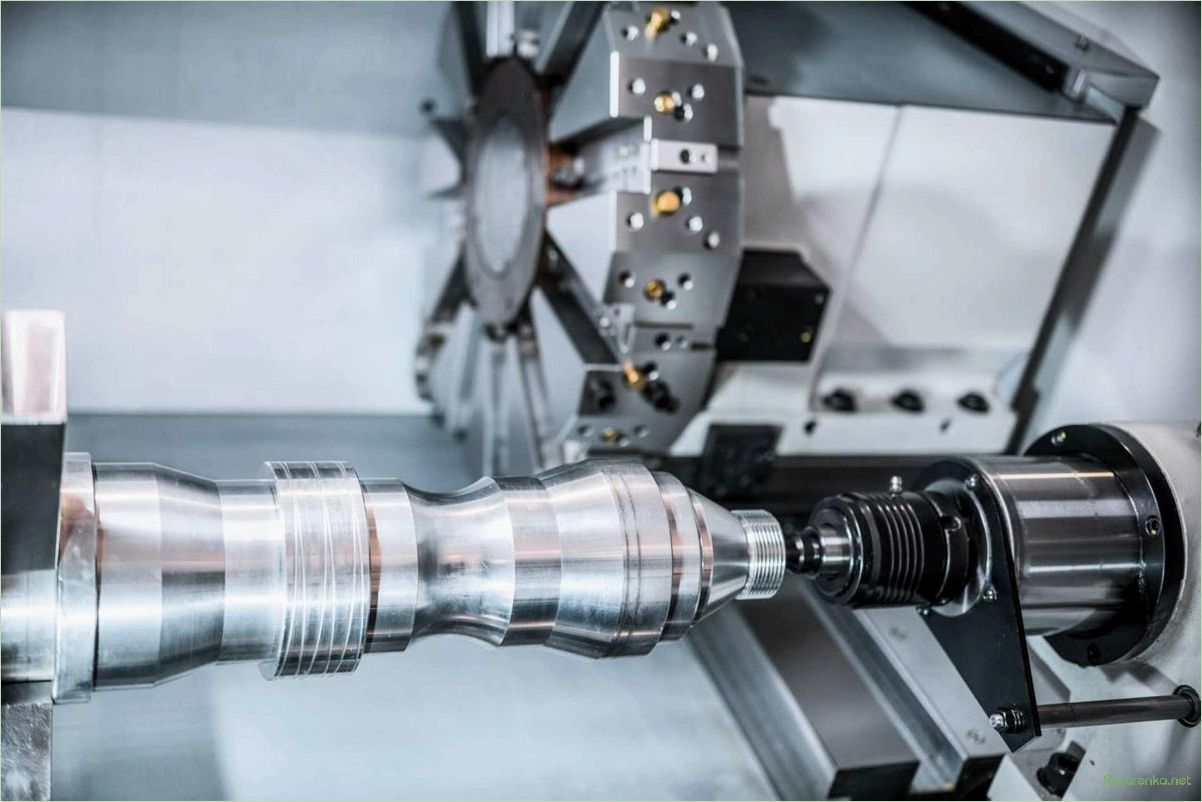
Токарная обработка является одним из основных процессов в металлообработке. Она позволяет создавать различные детали и изделия, обеспечивая высокую точность и качество поверхности. Токарные станки широко применяются в машиностроении, автомобильной и авиационной промышленности, а также в других отраслях производства.
Содержание статьи:
- Процесс обработки деталей на токарных станках
- Подготовка оборудования и инструментов
- Обзор основных операций токарной обработки
- Операция растачивания
- Операция подрезания
- Операция нарезания резьбы
- Операция точения
- Операция растачивания отверстий
- Операция нарезания пазов
- Операция обточки
- Операция резьбонарезания
- Операция шлифования
- Операция полировки
- Операция зенковки
- Операция развертывания
- Операция нарезания шестигранников
- Операция фрезерования
- Операция нарезания шпоночных пазов
- Выбор и подготовка сырья для обработки
- Настройка и запуск токарного станка
- Контроль качества обработки и финишная обработка деталей
Основным принципом работы токарного станка является вращение заготовки и инструмента вокруг своей оси. Инструмент срезает слой материала с поверхности заготовки, что позволяет получить требуемую форму и размер. Также с помощью токарных станков можно выполнять различные операции, такие как нарезка резьбы, сверление отверстий и обработка конических поверхностей.
Токарная обработка является одним из самых распространенных и важных методов обработки деталей. Она позволяет получить высокую точность и повторяемость результатов. Токарные станки обладают высокой производительностью и могут обрабатывать детали различной сложности и размеров.
Для выполнения токарной обработки необходимо правильно подобрать инструменты и настроить станок. Важным аспектом является выбор материала заготовки и определение оптимальных параметров обработки. Также необходимо учитывать требования по точности и качеству поверхности детали. Правильное выполнение всех этих шагов позволяет достичь высоких результатов и обеспечить эффективность процесса обработки.
Процесс обработки деталей на токарных станках
Токарные станки являются одним из основных инструментов в процессе обработки металлических деталей. Они позволяют осуществлять различные операции с деталями, такие как нарезание резьбы, точение, формование поверхности и другие.
Подготовка детали
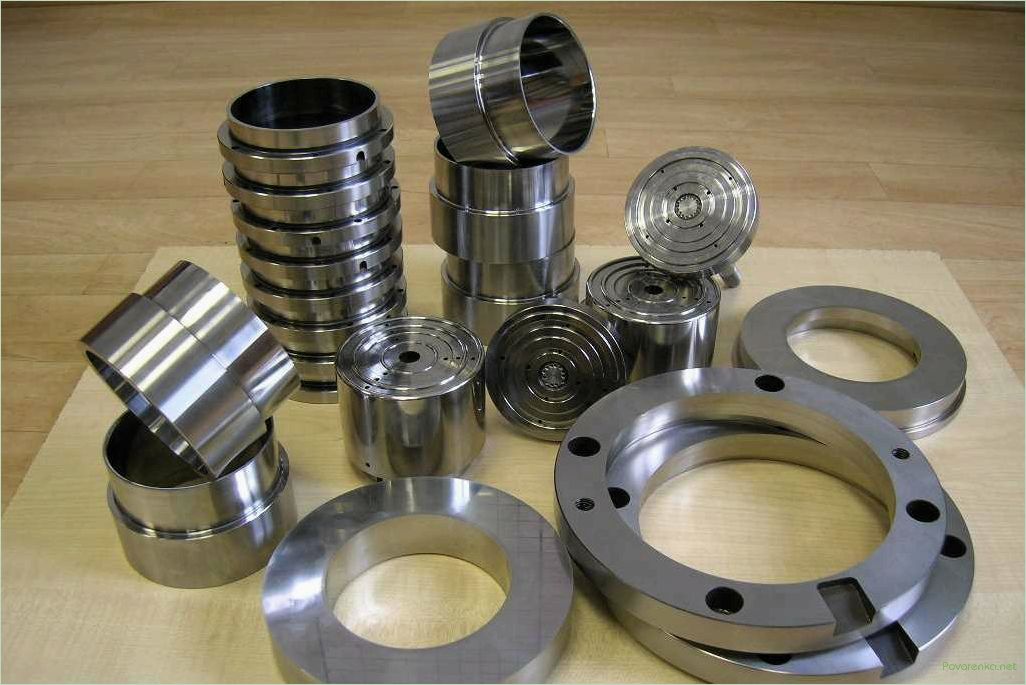
Перед началом обработки деталей на токарном станке необходимо провести их подготовку. Это включает в себя установку и закрепление детали на станке с помощью специальных приспособлений. Также необходимо проверить правильность установки и закрепления детали, чтобы избежать ее смещения в процессе обработки.
Выбор инструмента и настроек станка
После подготовки детали необходимо выбрать подходящий инструмент для выполнения требуемой операции. Это может быть режущий инструмент, такой как резец или сверло, или специальное приспособление для формования поверхности. Также необходимо настроить параметры станка, такие как скорость вращения шпинделя, подачу инструмента и глубину резания.
Выполнение операции
После выбора инструмента и настройки станка можно приступать к выполнению операции обработки детали. Операция может включать в себя движение инструмента вдоль оси детали, вращение детали вокруг своей оси или их комбинацию. В процессе обработки детали необходимо следить за точностью и качеством выполняемой операции, а также за состоянием инструмента.
Контроль качества
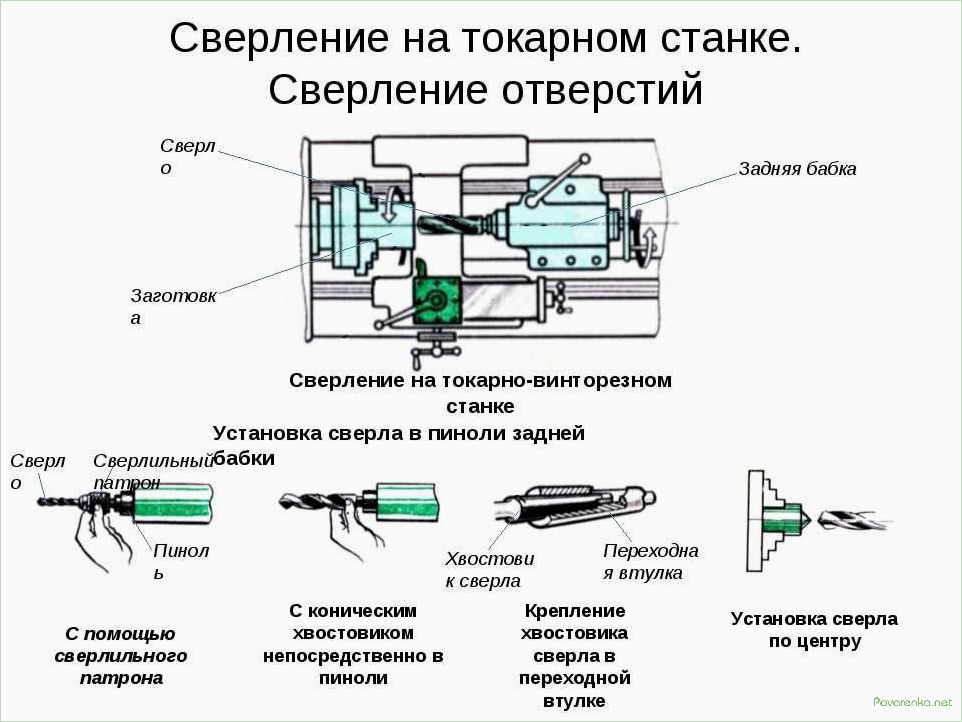
По завершении операции обработки детали необходимо провести контроль качества полученной детали. Это может включать в себя измерение размеров и формы детали, проверку наличия дефектов и соответствия требуемым техническим характеристикам. Если деталь не соответствует требованиям, необходимо провести дополнительные операции для ее исправления.
Заключение
Процесс обработки деталей на токарных станках является важным этапом в производстве металлических изделий. Правильная подготовка детали, выбор подходящего инструмента и настройка станка, а также контроль качества позволяют получить высококачественные детали с требуемыми характеристиками.
Подготовка оборудования и инструментов
Перед началом обработки деталей на токарных станках необходимо провести подготовительные работы, включающие в себя проверку и настройку оборудования, а также подготовку необходимых инструментов.
Проверка оборудования
Перед началом работы следует убедиться в исправности и готовности к использованию токарного станка. Проверка оборудования включает в себя следующие шаги:
- Проверка электропитания: убедитесь, что токарный станок подключен к электрической сети и имеет стабильное напряжение.
- Проверка рабочих инструментов: убедитесь, что все необходимые инструменты находятся на своих местах и готовы к использованию.
- Проверка системы охлаждения: убедитесь, что система охлаждения токарного станка функционирует должным образом и имеет достаточное количество охлаждающей жидкости.
- Проверка системы смазки: убедитесь, что система смазки токарного станка работает исправно и имеет достаточное количество смазочного материала.
Подготовка инструментов
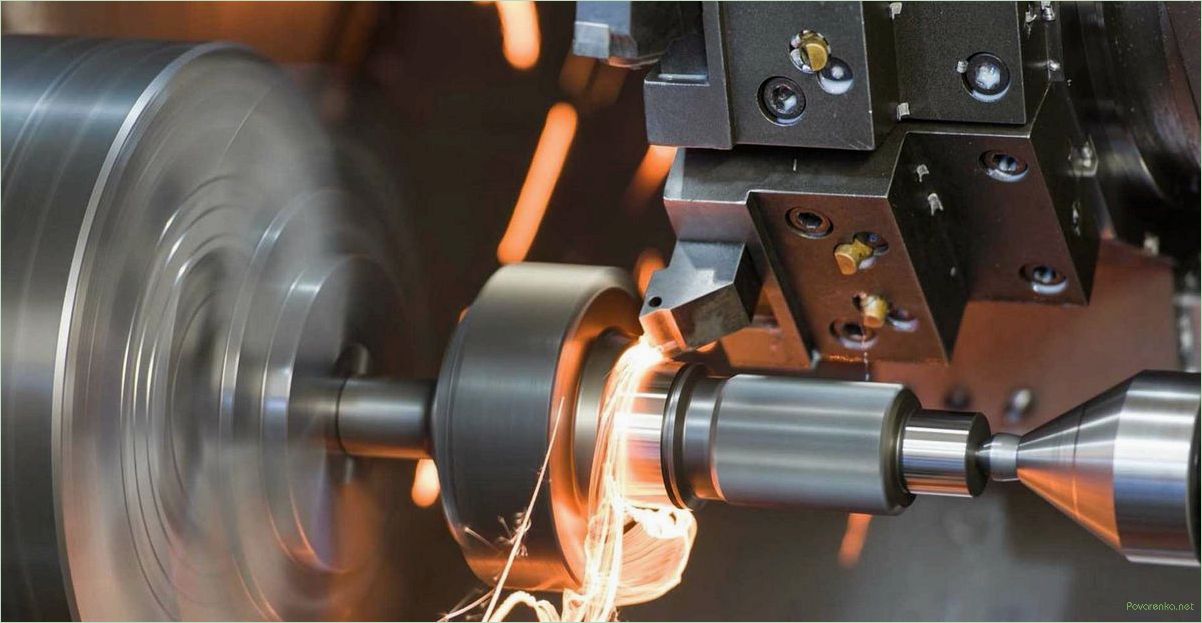
Подготовка инструментов включает в себя следующие этапы:
- Выбор необходимых инструментов: определите список инструментов, которые будут использоваться при обработке деталей на токарном станке.
- Проверка состояния инструментов: осмотрите инструменты на наличие повреждений, износа или других дефектов. Поврежденные инструменты следует заменить.
- Заточка инструментов: при необходимости заточите инструменты, чтобы они были готовы к использованию.
Правильная подготовка оборудования и инструментов перед началом работы на токарном станке позволяет избежать непредвиденных ситуаций, повышает качество обработки деталей и обеспечивает безопасность оператора.
Обзор основных операций токарной обработки
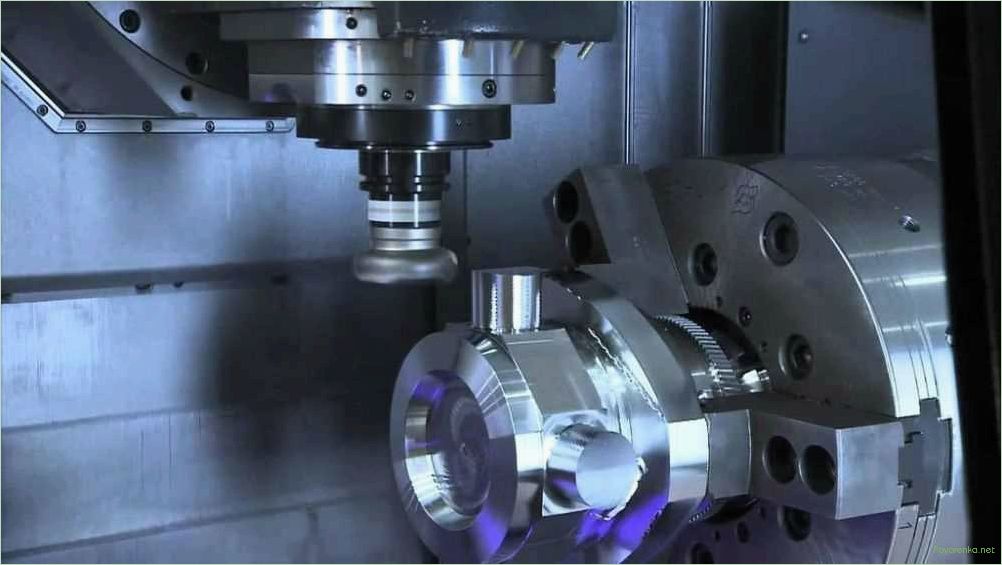
Токарная обработка — это один из основных способов механической обработки деталей на токарных станках. Она позволяет получать детали с заданными геометрическими параметрами и поверхностной шероховатостью. В процессе токарной обработки применяются различные операции, которые выполняются последовательно для достижения требуемого результата.
Операция растачивания
Растачивание — это операция удаления излишков материала с поверхности детали. Она выполняется с помощью режущего инструмента — резца. Резец устанавливается на токарный станок и, двигаясь по заданной траектории, удаляет слой материала. Растачивание позволяет получить нужную форму и размеры детали.
Операция подрезания
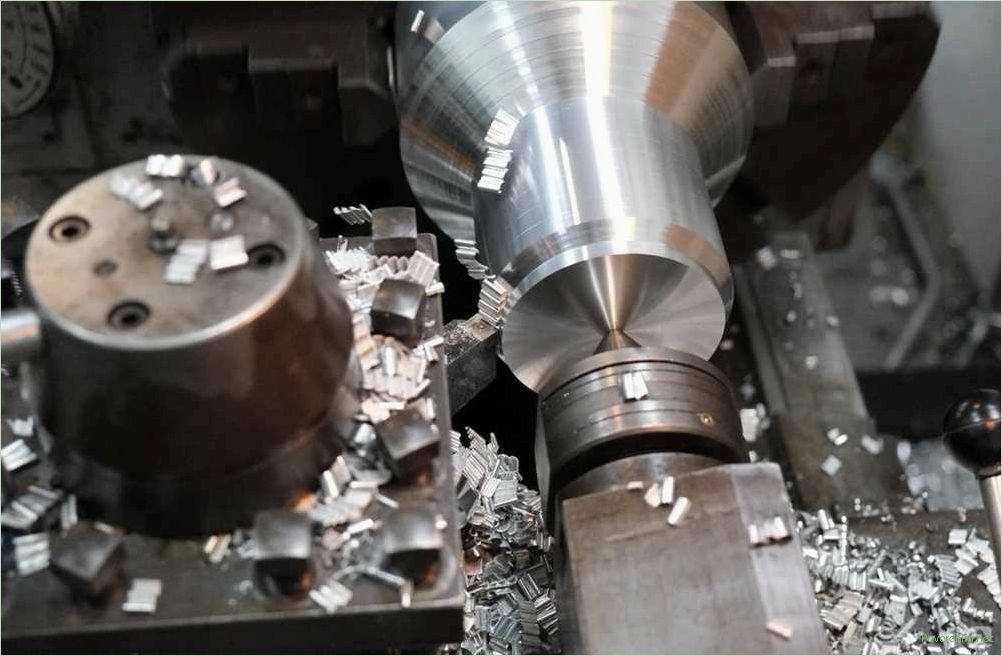
Подрезание — это операция удаления избыточного материала с торцов детали. Она выполняется с помощью специального инструмента — подрезного резца. Подрезной резец устанавливается на токарный станок и обрабатывает торцовую поверхность детали, удаляя излишки материала и придавая торцу нужную форму и шероховатость.
Операция нарезания резьбы
Нарезание резьбы — это операция создания резьбового профиля на внешней или внутренней поверхности детали. Для нарезания резьбы используется специальный режущий инструмент — нарезной плашка. Плашка снабжена резьбовыми зубьями, которые вырезают резьбовой профиль при движении по поверхности детали. Нарезание резьбы позволяет создавать соединения с помощью болтов, гаек и других резьбовых элементов.
Операция точения
Точение — это операция обработки внешней поверхности детали. Она выполняется с помощью режущего инструмента — точильного резца. Резец устанавливается на токарный станок и, двигаясь по заданной траектории, удаляет слой материала с внешней поверхности детали. Точение позволяет получить нужную форму и шероховатость внешней поверхности.
Операция растачивания отверстий
Растачивание отверстий — это операция создания отверстий требуемого диаметра и глубины в деталях. Она выполняется с помощью специального инструмента — растачивающего резца. Резец устанавливается на токарный станок и, двигаясь по заданной траектории, вырезает материал, создавая отверстие. Растачивание отверстий позволяет получать отверстия с точными размерами и шероховатостью.
Операция нарезания пазов
Нарезание пазов — это операция создания пазов на внешней или внутренней поверхности детали. Для нарезания пазов используется специальный режущий инструмент — нарезной плашка. Плашка снабжена режущими зубьями, которые вырезают пазы при движении по поверхности детали. Нарезание пазов позволяет создавать соединения с помощью шпоночных соединений и других пазовых элементов.
Операция обточки
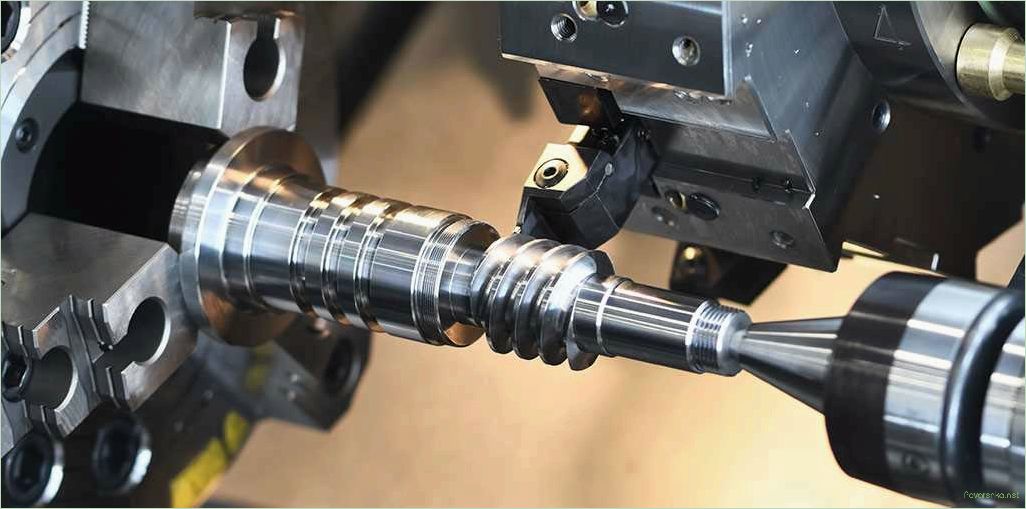
Обточка — это операция удаления излишков материала с поверхности детали с целью придания ей точной формы и шероховатости. Обточка выполняется с помощью режущего инструмента — обточного резца. Резец устанавливается на токарный станок и, двигаясь по заданной траектории, удаляет слой материала с поверхности детали. Обточка позволяет получать детали с высокой точностью и качеством поверхности.
Операция резьбонарезания
Резьбонарезание — это операция создания резьбы на внешней или внутренней поверхности детали. Для резьбонарезания используется специальный режущий инструмент — резьбонарезной плашка. Плашка снабжена режущими зубьями, которые вырезают резьбовой профиль при движении по поверхности детали. Резьбонарезание позволяет создавать соединения с помощью болтов, гаек и других резьбовых элементов.
Операция шлифования
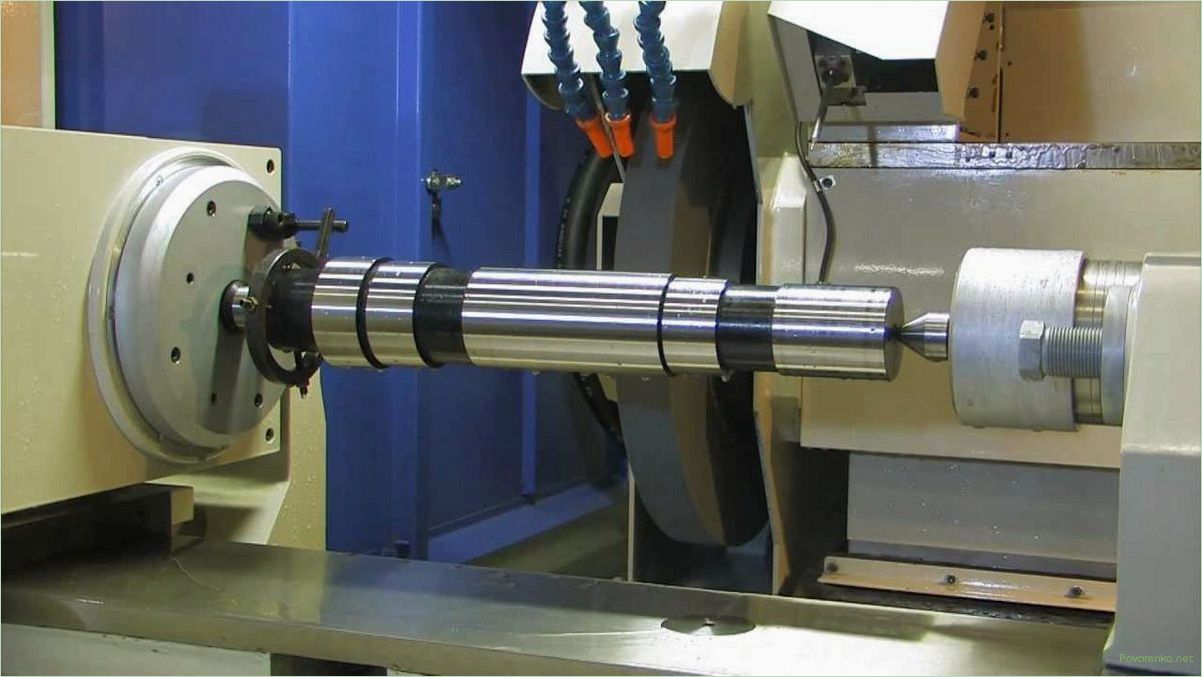
Шлифование — это операция удаления тонких слоев материала с поверхности детали с целью придания ей высокой точности формы и шероховатости. Шлифование выполняется с помощью абразивного инструмента — шлифовального круга. Круг устанавливается на токарный станок и, двигаясь по поверхности детали, удаляет тонкий слой материала. Шлифование позволяет получать детали с очень высокой точностью и качеством поверхности.
Операция полировки
Полировка — это операция придания поверхности детали высокой шероховатости и блеска. Полировка выполняется с помощью специальных полировальных средств и инструментов. В процессе полировки на поверхности детали обрабатываются мелкие дефекты и несовершенства, придавая поверхности гладкость и блеск.
Операция зенковки
Зенковка — это операция создания заглубления в детали для установки головки винта, шпильки или другого элемента соединения. Для зенковки используется специальный инструмент — зенковка. Инструмент устанавливается на токарный станок и, двигаясь по поверхности детали, вырезает заглубление. Зенковка позволяет создавать точные и надежные соединения между элементами.
Операция развертывания
Развертывание — это операция увеличения диаметра отверстия в детали. Она выполняется с помощью специального инструмента — развертки. Инструмент устанавливается на токарный станок и, двигаясь по поверхности детали, увеличивает диаметр отверстия. Развертывание позволяет получать отверстия с заданными размерами и шероховатостью.
Операция нарезания шестигранников
Нарезание шестигранников — это операция создания шестигранного профиля на внешней или внутренней поверхности детали. Для нарезания шестигранников используется специальный режущий инструмент — шестигранная нарезная плашка. Плашка снабжена режущими зубьями, которые вырезают шестигранник при движении по поверхности детали. Нарезание шестигранников позволяет создавать соединения с помощью гаек и болтов с шестигранной головкой.
Операция фрезерования
Фрезерование — это операция создания пазов, выточек и других элементов на внешней или внутренней поверхности детали. Она выполняется с помощью фрезерного инструмента — фрезы. Фреза устанавливается на токарный станок и, двигаясь по поверхности детали, вырезает необходимые элементы. Фрезерование позволяет создавать сложные геометрические формы и элементы на поверхности детали.
Операция нарезания шпоночных пазов
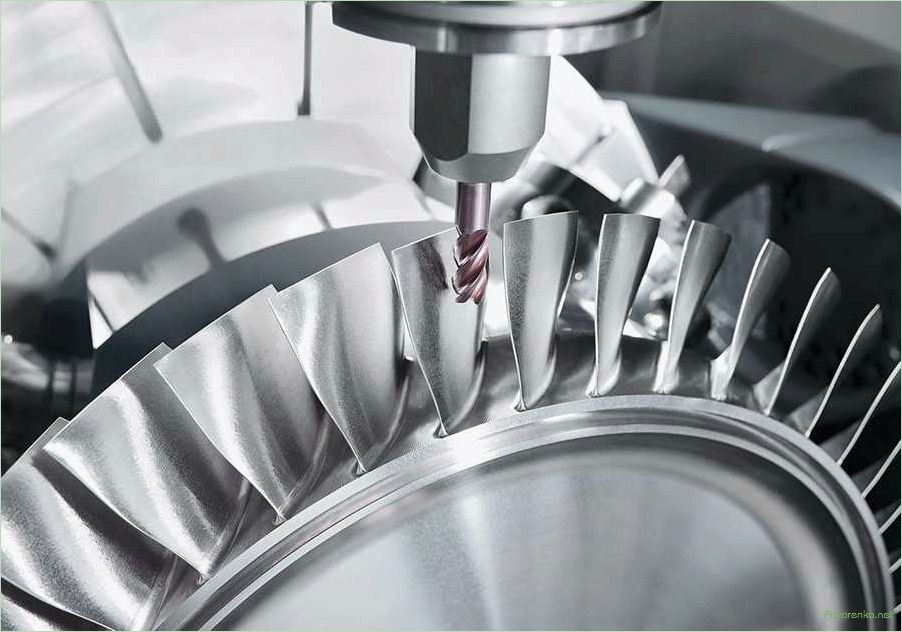
Нарезание шпоночных пазов — это операция создания пазов на внешней или внутренней поверхности детали для установки шпоночной соединительной детали. Для нарезания шпоночных пазов используется специальный режущий инструмент — шпоночная нарезная плашка. Плашка снабжена режущими зубьями, которые вырезают пазы при движении по поверхности детали. Нарезание шпоночных пазов позволяет создавать надежные соединения с помощью шпоночных элементов.
Сравнительная таблица основных операций токарной обработки
Операция | Описание |
---|---|
Растачивание | Удаление излишков материала с поверхности детали |
Подрезание | Удаление избыточного материала с торцов детали |
Нарезание резьбы | Создание резьбового профиля на поверхности детали |
Точение | Обработка внешней поверхности детали |
Растачивание отверстий | Создание отверстий требуемого диаметра и глубины |
Нарезание пазов | Создание пазов на поверхности детали |
Обточка | Удаление излишков материала с поверхности детали |
Резьбонарезание | Создание резьбы на поверхности детали |
Шлифование | Удаление тонких слоев материала с поверхности детали |
Полировка | Придание поверхности детали высокой шероховатости и блеска |
Зенковка | Создание заглубления в детали для установки элемента соединения |
Развертывание | Увеличение диаметра отверстия в детали |
Нарезание шестигранников | Создание шестигранного профиля на поверх |
Выбор и подготовка сырья для обработки
Подготовка сырья является важным этапом процесса обработки деталей на токарных станках. От правильного выбора и подготовки сырья зависит качество и точность обработки, а также эффективность работы станка.
Выбор сырья
При выборе сырья для обработки на токарных станках необходимо учитывать следующие факторы:
- Материал детали: В зависимости от материала детали, выбирается соответствующее сырье. Например, для обработки стали используется стальной пруток, для обработки алюминия — алюминиевый пруток и т.д.
- Требования к детали: Если требуется получить деталь с определенными свойствами (например, высокой прочностью или хорошей коррозионной стойкостью), необходимо выбрать сырье с соответствующими характеристиками.
- Технологические особенности: Некоторые материалы могут быть сложны для обработки на токарных станках из-за своей структуры или механических свойств. При выборе сырья необходимо учитывать такие особенности и выбирать материал, который лучше всего подходит для конкретной операции.
Подготовка сырья
После выбора сырья необходимо провести его подготовку перед обработкой на токарном станке. Этот процесс включает в себя следующие этапы:
- Размеры и форма: Сырье должно иметь необходимые размеры и форму для обработки на токарном станке. При необходимости проводится операция по подгонке размеров и формы сырья.
- Очистка от загрязнений: Сырье должно быть очищено от загрязнений, таких как грязь, пыль, жидкости и т.д. Это необходимо для обеспечения качественной обработки и защиты станка от повреждений.
- Поверхностная обработка: При необходимости проводится поверхностная обработка сырья, такая как шлифовка или обезжиривание. Это позволяет улучшить качество поверхности детали после обработки.
- Маркировка: Важным этапом подготовки сырья является его маркировка. На сырье наносятся метки, которые позволяют идентифицировать деталь и проводить ее отслеживание на протяжении всего процесса обработки.
Правильный выбор и подготовка сырья для обработки на токарных станках являются важными факторами, которые влияют на качество и эффективность процесса обработки деталей. Следуя указанным выше рекомендациям, можно добиться оптимальных результатов и повысить производительность работы станка.
Настройка и запуск токарного станка
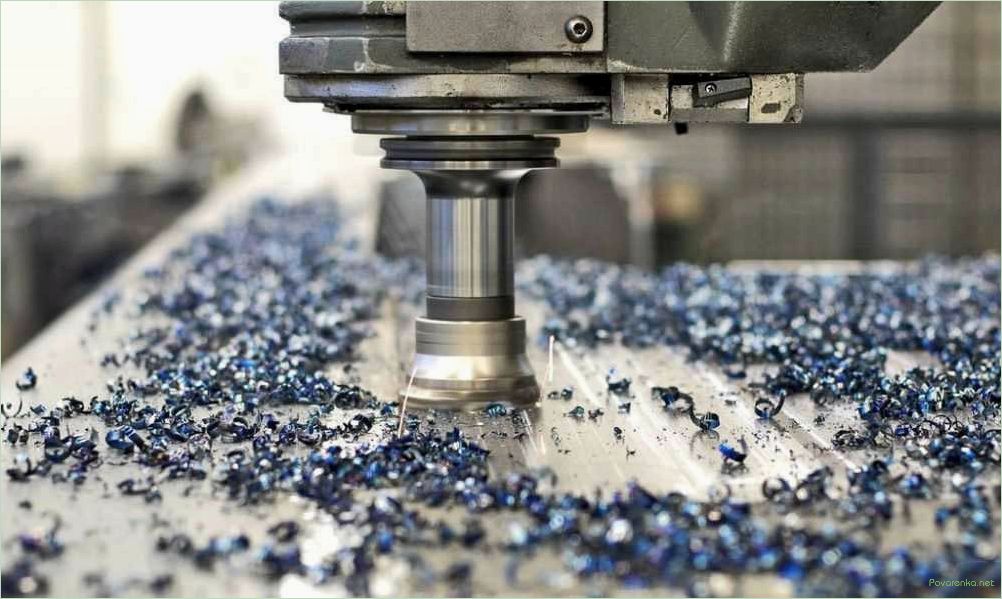
Настройка и запуск токарного станка являются важными этапами перед началом обработки деталей. Правильная настройка станка позволяет достичь высокой точности и качества обработки.
1. Подготовка рабочей зоны
Перед началом работы необходимо очистить рабочую зону от посторонних предметов и отходов. Также следует убедиться, что на рабочей поверхности станка нет повреждений или загрязнений, которые могут повлиять на качество обработки.
2. Проверка инструмента
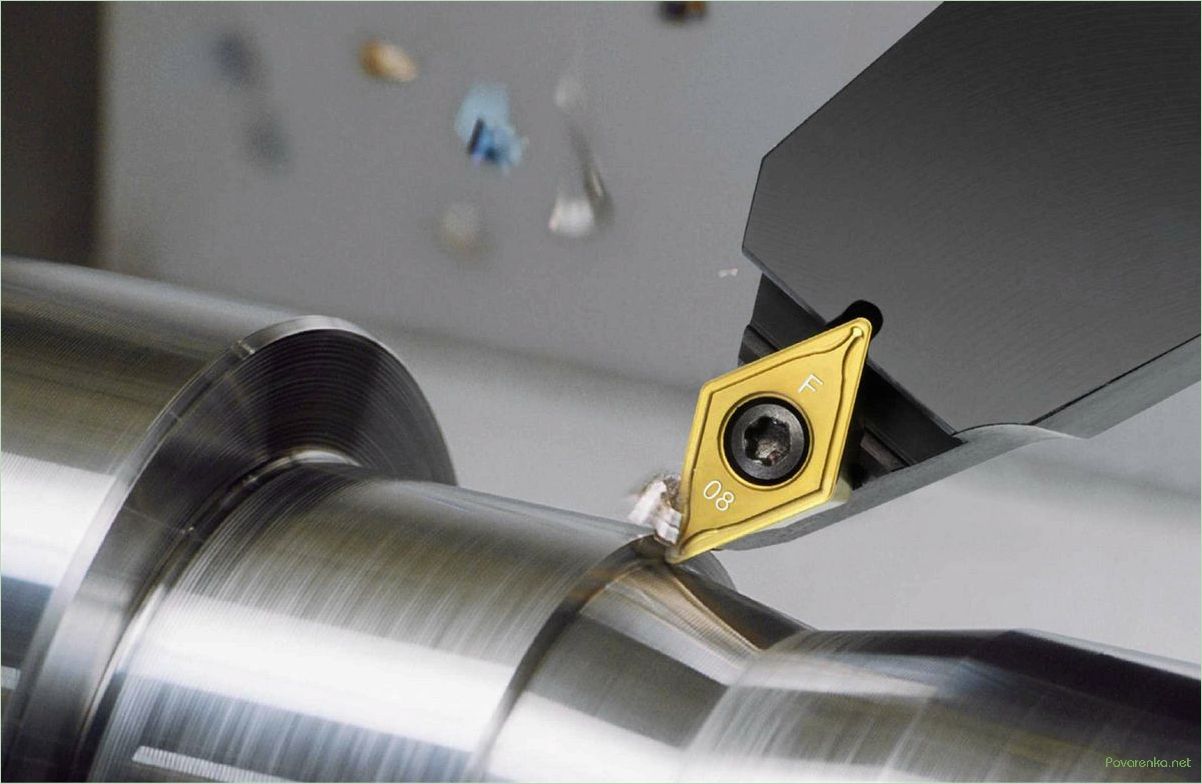
Перед установкой инструмента необходимо проверить его наличие, целостность и соответствие заданным параметрам. При необходимости следует заменить изношенный или поврежденный инструмент.
3. Установка и зажим детали
Для установки детали на токарный станок необходимо использовать специальные приспособления, такие как патроны, цанги или планки. При установке детали следует обеспечить надежное и точное зажимание, чтобы исключить возможность смещения или падения детали во время обработки.
4. Выбор режимов работы
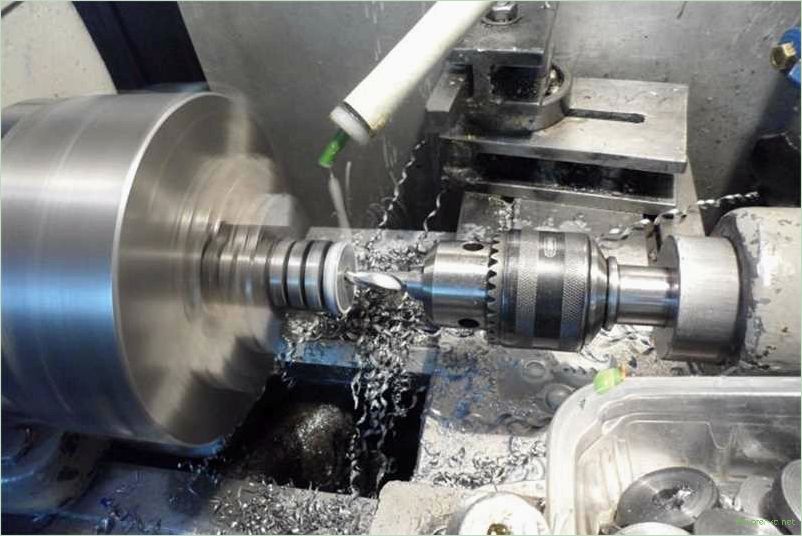
В зависимости от требований к обработке, необходимо выбрать оптимальные режимы работы токарного станка. Это включает выбор скорости вращения шпинделя, подачи инструмента, глубины резания и других параметров.
5. Запуск станка
После настройки всех параметров можно приступать к запуску токарного станка. Перед запуском следует убедиться в правильности настройки и зажиме детали. Постепенно увеличивая скорость, можно достичь рабочих значений и начать обработку детали.
Важно помнить, что настройка и запуск токарного станка требуют опыта и знаний. Неправильная настройка может привести к повреждению детали, инструмента или самого станка. Поэтому рекомендуется обратиться к специалисту или прошедшему обучение оператору, чтобы минимизировать риски и обеспечить качественную обработку деталей.
Контроль качества обработки и финишная обработка деталей
После проведения основной обработки деталей на токарных станках необходимо провести контроль качества полученных изделий, а также выполнить финишную обработку для достижения требуемой точности и гладкости поверхности.
Контроль качества обработки
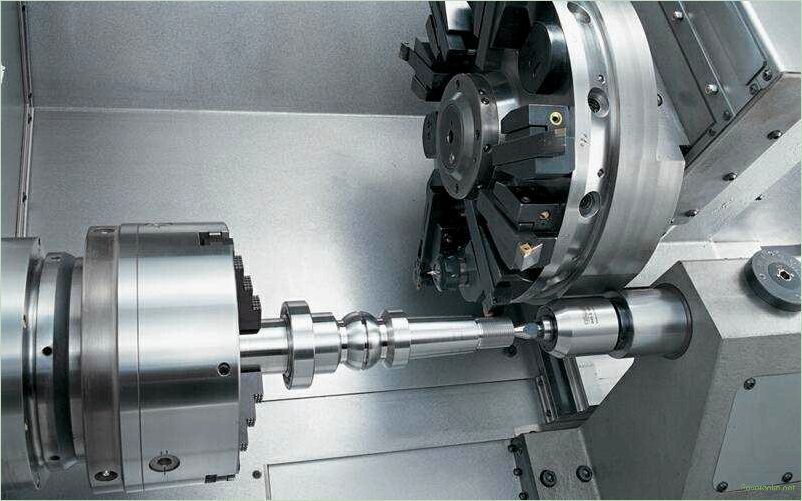
Контроль качества обработки деталей на токарных станках включает в себя следующие этапы:
- Визуальный контроль. На данном этапе осуществляется проверка наличия дефектов, таких как царапины, сколы, трещины и другие повреждения поверхности детали.
- Измерительный контроль. С помощью измерительных инструментов, таких как микрометры, штангенциркули, измеряются геометрические параметры деталей, такие как диаметры, ширины, глубины и т.д. При этом сравниваются полученные значения с требуемыми.
- Функциональный контроль. Здесь проверяется соответствие деталей заданным функциональным характеристикам. Например, проверяется работоспособность подшипников, соединений и других элементов, а также соответствие параметров деталей требуемым нагрузкам и условиям эксплуатации.
Финишная обработка деталей
Финишная обработка деталей на токарных станках выполняется для достижения требуемой точности и гладкости поверхности. Она включает в себя следующие операции:
- Шлифовка. Для удаления оставшихся после основной обработки дефектов поверхности детали используется шлифовальный инструмент. Это позволяет получить более гладкую поверхность и улучшить точность размеров.
- Полировка. При помощи полировальных инструментов и абразивных материалов деталь обрабатывается до зеркального блеска. Полировка также улучшает точность размеров и повышает эстетический вид изделия.
- Нанесение защитного покрытия. Для защиты поверхности детали от коррозии и износа может быть нанесено специальное покрытие, например, хромирование или никелирование.
После проведения финишной обработки детали готовы к использованию и соответствуют требованиям качества и внешнему виду.